What is TQM - Total Quality Management?
- Mech n Flow
- Jan 7, 2022
- 3 min read
Is it really useful?
Table of Contents:
You have probably heard of the phrase "Customer is the King"! Do you remember the last time someone treated you the exact opposite and you never went back to that place (except for a bank :))? Respecting the customer is the best way to make good relations with the customer, and in turn, improve your business. Total Quality Management (TQM) is exactly that.
What is TQM?
A core definition of total quality management (TQM) describes a management approach to long-term success through customer satisfaction.
The word "total" in TQM describes that everyone is involved in the process of "quality" and not just one particular department. Every employee takes the responsibility to serve better quality of product or service to the customer continuously.
Total Quality Management Principles
There is no perfect "recipe" for TQM. It is something an organization should apply as per their requirements and convenience. TQM sets the same work culture from top to down in management. But still, there are 8 principles to improve customer satisfaction continuously.
Customer Satisfaction: Ultimately customers should be satisfied for the business to grow. That's when the customers will come back and be loyal to your products or services and will determine the quality of the product or service.
Employee Commitment: The employees should work towards the common goals, follow the same organizational culture. The employees/teams should be self-driven towards the goal.
Process-Centered: The process is followed and the necessary steps are carried out while keeping track of the measurements.
Integrated System: Every employee in the organization should be connected to every part of the department. Having common goals and a shared vision.
Strategic Planning: A critical part of the management of quality is the strategic and systematic approach to achieving an organization’s vision, mission, and goals. This includes the formulation of a strategic plan that integrates quality as a core component.
Fact-Based Decision Making: Teams collect data and process statistics to ensure that work meets specifications.
Effective Communications: There should be an open dialogue throughout an organization.
Continuous Improvement: This is a very important principle. Improving continuously for fulfilling the needs of the customer should be every employee's aim always.
Why is TQM needed?
TQM helps align all the employees of the organization to have the same organizational culture and goal. With the focus on customer satisfaction, the product or service quality increases. The benefits of TQM are as follows:
Customer satisfaction
Fewer product defects
Improvement of quality
Lower costs
Good culture organization-wide.
Deming’s 14 Points on Quality Management
Deming came up with 14 points to improve the quality of the product or service. After World War II, during the economic crisis, Japan's quality of products was increasing drastically, due to these 14 points proposed by Deming.

Tata Steel, a steel-making company based in India, adopted TQM in the 1980s. Tata Steel used TQM methodologies to gain a deep understanding of customers.
In 2008, Tata Steel created the Performance Improvement Committee (PIC) to drive continuous performance improvement. Performance Improvement (PI) Groups were established for iron making, steel making, flat rolling, long rolling, maintenance, and more.
As part of their 2008-2009 annual report, Tata Steel reported that their TQM initiatives resulted in a $150MM impact on their business.
History
The history of TQM dates back to the 1980s, and actually, no one is sure who initiated it. Is it, Kaoru Ishikawa or William Deming? Moreover, innovation came in the 1920s with Walter Shewhart’s elaboration of statistical process controls, which one could apply at any point in the production process to predict quality levels. Post World War II, Japan implemented TQM and the quality of Japanese products began to improve. They began to include workmen in their quality process and saw tremendous growth.
Later everyone adopted this approach and it becomes the foundation of the quality process. But the use of TQM is not too widespread today due to competition from other quality management systems such as Lean Manufacturing, Six Sigma, and the ISO 9000 series.
Summary
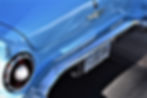
A core definition of total quality management (TQM) describes a management approach to long-term success through customer satisfaction.
TQM is no longer used directly but is the foundation of quality management.
The practice of TQM obtains customer satisfaction, fewer product defects, improvement of quality, lower costs, and good culture organization-wide.
Short Video
Happy New year everyone! I cannot believe MechnFlow completed one year already. I am so happy we never gave up on this one. Thank you team for being with me and handling all of my tantrums. Hope you have more years and all coming years with you all!